
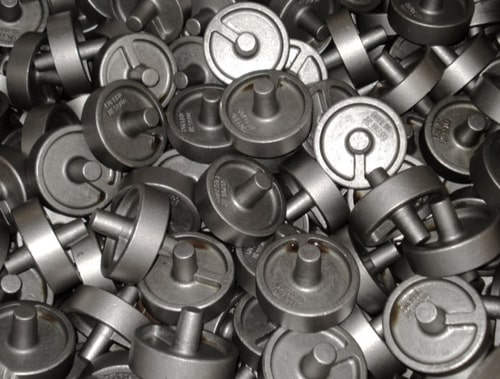
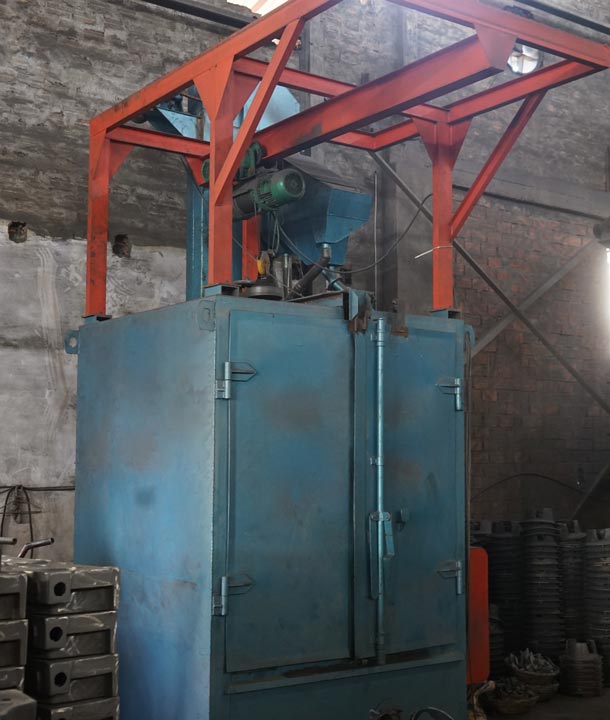
The full surface of the castings is made uniform and clean. In the fettling step, the adhering sand and unnecessary projections from the metal are removed.Castings are taken out by breaking the molds before they are delivered to the cleaning section.The molds are then left to cool, and the liquid metal solidifies in the mold. Liquid metal is ladled into the molds.Metal with the proper composition is melted in the appropriate furnace.Proper mold design for the flow of liquid metal is essential for the production of accurate castings.The molding may be carried out either by hand or with the aid of machines. The cores and molds are baked to convey strength and finally joined for pouring. To create a hollow part, cores are made in core boxes.A pattern is used to produce a cavity of the required shape. The patterns are delivered to the molding step, where molds are made in either sand or another material.The materials utilized for pattern making are metal, wood, or plastics.The objects of the pattern are chosen based on factors like the number of castings needed and the surface finish required.Patterns are prepared as directed by the drawing of the casting acquired from the planning stage and in accordance with the molding process.The following are the processes of producing metal casting: Pattern Making Products with multifaceted shapes, hollow sections, multifaceted internal cavities, and unevenly curved surfaces made from metals that are hard to machine are simple to produce with the casting procedure. The castings can be produced in dimensions ranging from a few millimeters to many meters and may weigh from a few grams to several tons. It is the first stage in manufacturing many products.Ĭasting is created from any meltable metal and can have any form the designer wants. Now, all we have to do is get the cookware to you.The metal casting procedure is the earliest and most popular means of manufacturing designs in certain shapes. Our employees give the cookware a final inspection before packing it with biodegradable paper and corrugated packing material. This creates a natural, easy-release finish that gets better with use. Our cookware is then sprayed with vegetable oil and baked at a high temperature, well above the range of a typically household oven. First, they go through a hot rinse and hot air blow off. Once the cast iron is completely cleaned, it’s hung on a conveyor to be seasoned. The stainless steel media is designed to come into complete contact with every inch of the skillet for a deep clean. Next, the cookware will fall into a bath of stainless steel media, soap, and water to enhance the finish. Inside the machine, the cookware is blasted from all sides. Our cookware is cleaned with fine steel shot. The iron media is specifically engineered to break up the sand and scrub it from the casting surface. The cookware enters a rotating drum, filled with iron media. Now, in the final step of the finishing process before boxing, Lodge cookware is sprayed with soybean oil and baked at a high temperature, creating a ready-to-use, easy-release surface. The water-soluble wax had to be washed off at home, then the cookware had to be oiled and baked in the oven before it could be used. Prior to this, cast iron was sold unseasoned, with a thin layer of carnauba bean wax to prevent rust during storage and merchandising. In 2002, Lodge debuted seasoned cast iron cookware - an industry first. During the 1970s, Lodge renovated the foundry with steel columns, a new roof, and a new exterior. This innovative machinery fully automated the casting process and greatly improved production capabilities. In 1965, Lodge became the first American company to use a Disamatic, a Danish molding machine that had once been used for manufacturing during World War II. This created a safer working environment for foundry workers. The foundry converted from a hand-pour operation to an automated molding process in 1950.
